How A Lens is Designed in Zemax
I start a design in Zemax by entering fundamental optical constraints, such as spectral band, aperture size, field of view, image size, etc. I also create a catalog of glasses and other lens materials that can be used in the design. I impose many additional constraints, such as minimum and maximum lens thickness, lens spacing, and max distortion. In addition, I select an image quality criterion, such as wavefront error (WFE), modulation transfer function (MTF), or spot size.
Once that’s all configured, the Zemax optimizer adjusts lens positions, curvatures, glass types, and so on to meet all the design constraints as well as it can, while simultaneously improving the image quality.
At any time during this process, I can evaluate the performance, but note that this is the “nominal” performance, as if every lens were perfectly fabricated and aligned. In actuality, the lenses will be fabricated and mounted to within certain manufacturing tolerances that I will specify in my lens drawings. Tolerancing analysis is how I determine what those tolerances should be.
Sensitivity Analysis and Tolerance Desensitization in Zemax
The first step is a quick sensitivity analysis. I enter tolerance ranges for each lens fabrication and mounting parameter based on what I estimate to be the appropriate quality grade (i.e., commercial, standard precision, or high precision). I also define a compensator. That’s the detector position by default, but it can be any parameter.
Zemax statistically evaluates the impact of each tolerance on the image quality, estimates the impact of all tolerances combined, and identifies the most stressing tolerances. I can then either tighten up the tolerances for those worst offenders or run a new optimization that attempts to reduce the sensitivity to them.
Monte Carlo Tolerance Analysis
In order to get a more realistic assessment of the performance with tolerances, I run a series of Monte Carlo simulations in Zemax. Each simulation is a mock system in which every parameter (thickness, abbe number, etc.) has been randomly assigned a value within the tolerances I’ve specified.
From this analysis, I can more reliably predict the real world performance in terms of the merit function criterion. In addition to the basics, like MTF or WFE, I can evaluate many other image quality metrics, such as encircled energy, by writing a script.
One useful output of the Monte Carlo tolerance analysis is a histogram. In the example below, 1,000 builds were simulated. The median MTF is expected to be around 0.54. A few builds are expected to have MTFs between 0.37 and 0.40 and at least 40 builds are expected to have MTFs > 0.57.
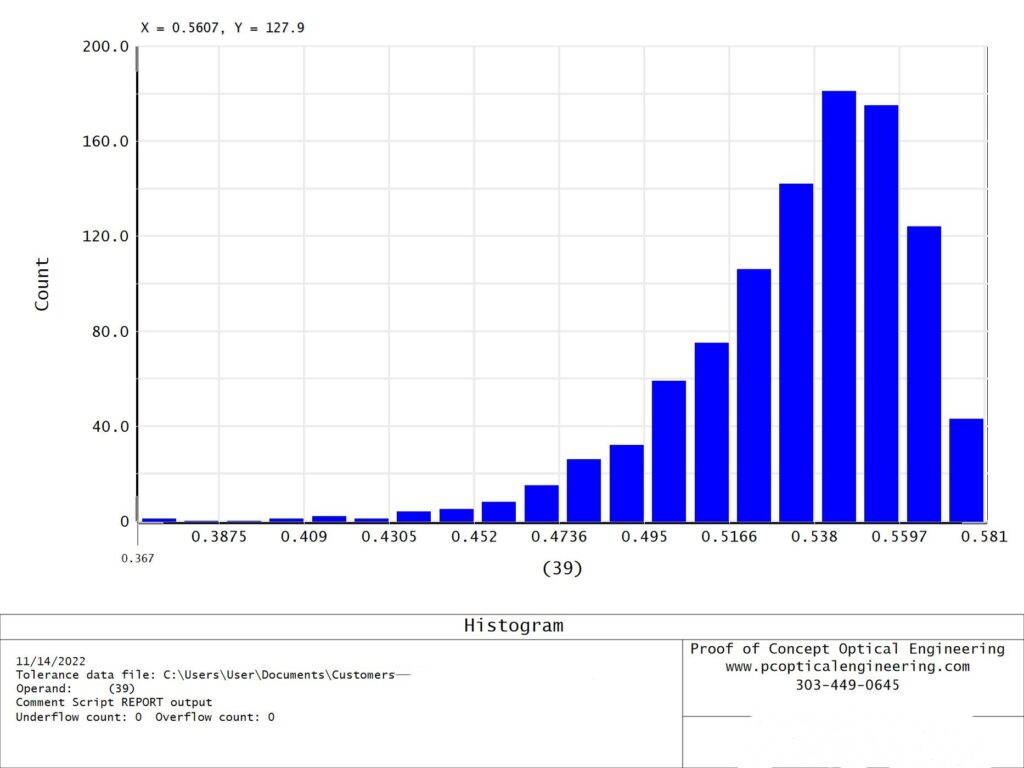
Another useful output is a yield curve. In the figure below, you can see that if the max allowable WFE is 0.38 waves, approximately 95% of the builds are expected to meet that requirement.
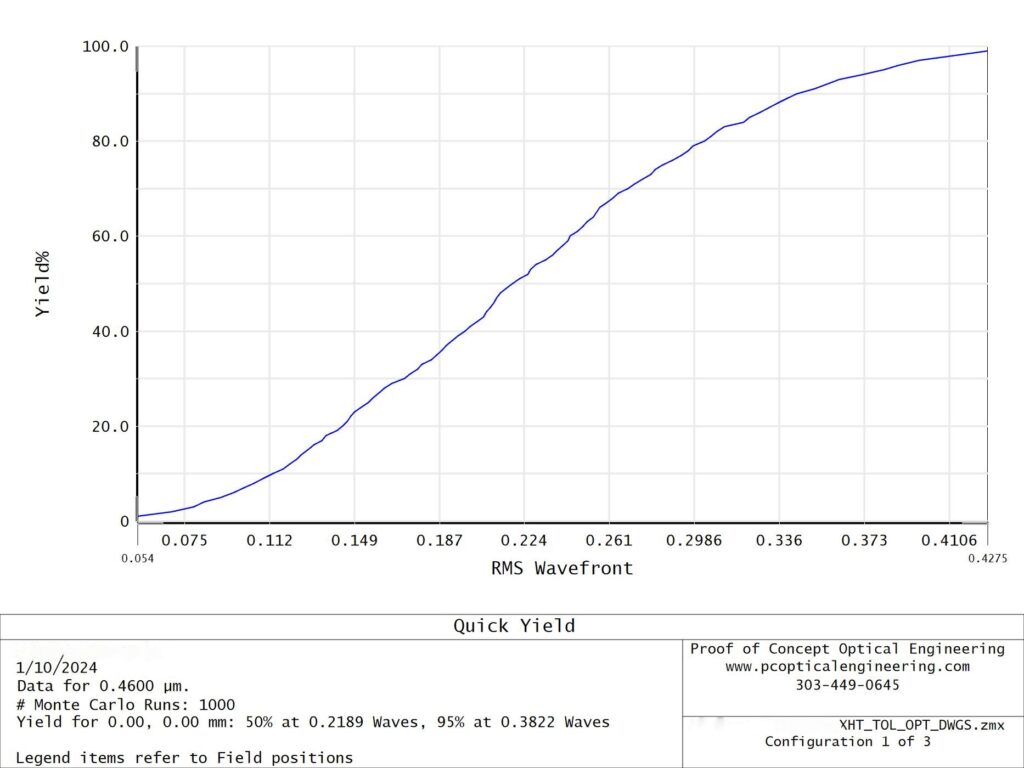
Cost Estimation
Once I’ve assigned tolerances to each lens parameter, I can estimate the cost of fabricating the optics. Zemax has a built in cost estimator I can use to estimate pricing for singlet lenses, but in most cases, I will need to submit my toleranced lens drawings to a vendor for a quote.
The vendor will need to know if we’re building just one system or 1000. I typically ask them to quote both, although the fabricators that reliably make high-quality prototypes are not usually the most cost effective option for production. I often recommend a different fabricator when we reach that stage in the product development process.
What’s the Budget Version of Tolerance Analysis?
At this point, I hope I’ve convinced you that a tolerance analysis is needed.
That said, I take a minimalist approach:
If preliminary Monte Carlo simulations show acceptable performance with standard precision tolerances, I can use those generic tolerances in the drawings. That’s usually fine for a prototype. To run that analysis and create drawings can take anywhere from a few hours to a day, depending on the system complexity.
If image performance expectations aren’t met with standard precision tolerances and the budget doesn’t allow for any high precision tolerances, I’ll need to desensitize the design, which is an iterative process.
Either way, if you’re planning to manufacture in volume, allowing me to spend some additional time evaluating which tolerances can be relaxed and considering additional compensation mechanisms will generally lower your fabrication costs by far more than the cost of those hours.